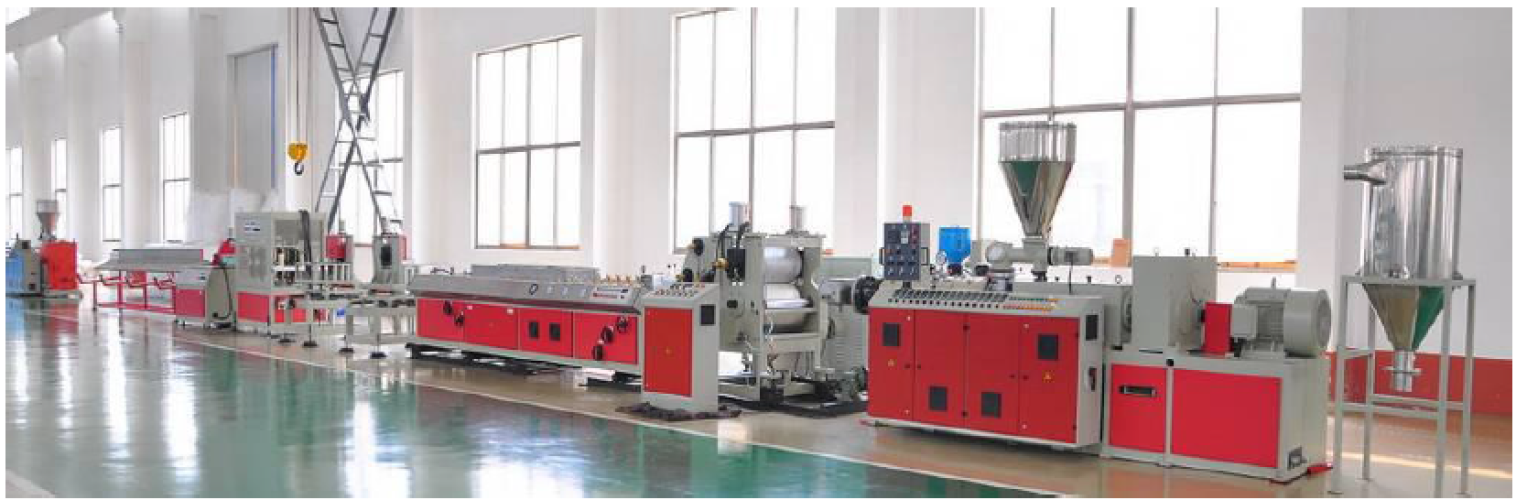
PVC Wood Plastic Composite Hollow Door Panel Making Machine
WPC hollow door panel is made of Wood plastic is a composite material and wood powder, it is environmental material and can be recycled and used repeatedly with the low cost of the raw material.
Wood-plastic composite products advantages
- Environmentalism
- Waterproof, dampproof, rotproof.
- Reasonable structure and high intensity
- Splicing structure, timesaving and laborsaving
- Finer heat preservation and sound insulation
- Stable quality and economical cost.
Wood-plastic composite door production Process
A. Technical Routes
Wood Power + PVC Resin + Assistant Agent → Extrusion → Forming → Printing on
Surface → Installation → Packaging
1-Feeding material unit |
2-Extruder |
3-Cooling and calibrating parts |
4-Draw-off unit |
5-Cutting machine |
6-Stacker |
B.Flow Chart
C. Technical introduction
Firstly put PVC, wood powder, compounding, and another assistant agent into high-speed mixer. After mixing
symmetrically and then deeding into the hopper. At the same time fix extruder temperature in advance and keep it.
Thirdly melting and plasticizing resin by specially designed screw symmetrically, and transporting into vacuum
forming system, and cooled. Then put into the draw-off system and reaching an automatic cutting system according to a fixed length, and cutting automatically to the stacker. Finally, pack the qualified product into storage. The defective products and edges will be recycled by crusher and flour milling.
D. Main Material
- PVC
- Wood powder
- Plugging compound
- Assistant agent
E.Detailed Specification
1. Crusher and Milling Machine(it is mainly used for wood, branches, etc)
Material | sawdust, cob, wood shavings, straw, etc | |
Material moisture | content 10% below | |
Wood Kernel | 40 item-100item | |
Output about | 400KG/h(≥80 mesh) | |
Total power | 100.8kw | |
Energy consumption | approx 75kw/h | |
Dimension | (L*W*H)(approx) 8.7×3×4.8m | |
Total weight | (approx) 5T |
2.High-Speed Mixer
Capacity | 300/600L | |
Effective capacity | 150/320L | |
Blade speed | 475/950/130 m/min | |
Motor&Heating | 30/42/11KW | |
Mixing&Cooling time | 6-8/8-10 S | |
Heating method | Electric heating/Friction | |
Discharge method | Manually/Pneumatic | |
Dimension | (L*W*H)(approx) 8.7×3×4.8m | |
Total weight | (approx) 5T |
3. High-Speed Mixer
Capacity | 500/1000L | |
Effective capacity | 375/640L | |
Blade speed | 430/260/50 m/min | |
Motor&Heating | 47/67/18.5KW | |
Mixing&Cooling time | 6-8/8-10 S | |
Water consumption | 7.8T/h | |
Air consumption | 0.40 m3/ min | |
Heating method | Electric heating/Friction | |
Discharge method | Manually/Pneumatic | |
Dimensions | 5580/2700/3432 | |
Total weight | 5.8T |
4. WPC Profile Production Line
A. Conical Double Screw Extruder Specialized for Wood Plastic
a> Screw | |
Material of screw | 38CrMoAlA high-grade alloy steel processed by nitriding |
Screw Dia. | Φ51/105mm |
Number | 2 pieces |
Meshing type | conical meshing |
Rotation speed | 1-32r/min |
Rotation direction | reverse direction outside |
Nitriding depth | 0.4-0.6mm |
Hardness degree | HV740-940 |
Surface roughness concentration | Ra≤0.8μm |
b> Hopper | |
Hopper material | 38CrMoAlA high-grade alloy steel processed by nitriding |
Nitriding depth | 0.5-0.7mm |
Hardness degree | HV940-1100 |
Inner roughness degree | Ra≤0.8μm |
Heating method | cast-aluminum electrical heater |
Heating zone | 4 zones |
Heating power | 8KW |
Cooling method | cooled by blower |
Cooling power | 3×250W |
c> Transporting deceleration system | |
Main extruder driving power | 15KW |
Motor type | AC motor |
Motor speed adjust the type | transducer speed adjust |
Splitter gearbox type | grinding gear combine with skew gear for the rigid gear surface |
d> Fixed amount feeding material system | |
Feeding material system | automatic quantify feeding by screw |
Screw rotation speed | 0-45r/min |
Motor driving | 0.75KW |
Speed adjust method | transducer adjust |
e> Exhausting system | |
Vacuum pump type | water recycling vacuum pump |
Motor power | 1.5KW |
Vacuum degree | 0-0.075Mp |
B. MXD180 Wood Plastic Vacuum Forming Machine |
|
Vacuum forming length | 4m |
Material water box | tank stainless steel |
Adjusting direction | three dimensional adjust |
Vacuum pump driving power | 2 sets × 5.5KW |
Pressure increasing pump power | 1.5KW |
Draining pump power | 0.75KW |
Vacuum connector | 32 pieces |
Water connector | 32 pieces |
Water consumption | 7m3/h |
C. Draw-off Machine |
|||
Draw-off type | rubber block drawing-off | ||
Rubber block type | drawing type | ||
Draw-off power | 2×1.5KW | ||
Draw-off strength | 40KN | ||
Draw-off speed | 0-5m/min | ||
The effective length of the draw-off roller | 1580mm | ||
Effective draw-off width | 180mm | ||
Working pressure | 0.5-0.7Mpa | ||
D. Cutting Machine |
|||
Max. cutting width | 200mm | ||
Cutting type | alloy saw cutting | ||
Saw dia. | 300mm | ||
Cutting power | 2.2KW | ||
Controlling method | automatically measure length | ||
E. Automatic Turning Over Shelf |
|||
Turning over shelf length | 6m | ||
Turning over method | automatic turning over | ||
Turning over shelf material | stainless steel | ||
Dimension | (L*W*H)(approx) 25×2×2m | ||
Total weight | (approx) 6T |
5. WPC Profile Production Line
A. Conical Double Screw Extruder Specialized for Wood Plastic
a> Screw | ||
Material of screw | 38CrMoAlA high-grade alloy steel processed by nitriding | |
Screw Dia. | Φ65/132mm | |
Effective length | 1440mm | |
Number | 2 pieces | |
Meshing type | conical meshing | |
Rotation speed | 1-34.7r/min | |
Rotation direction | reverse direction outside | |
Nitriding depth | 0.4-0.6mm | |
Hardness degree | HV740-940 | |
Surface roughness concentration | Ra≤0.8μm | |
b> Hopper | ||
Hopper material | 38CrMoAlA high-grade alloy steel processed by nitriding | |
Depth | 0.5-0.7mm | |
Hardness degree | HV940-1100 | |
Inner roughness degree | Ra≤0.8μm | |
Heating method | cast-aluminum electrical heater | |
Heating zone | 4 zones | |
Heating power | 24KW | |
Cooling method | cooled by blower | |
Cooling power | 3×250W | |
c>Transporting deceleration system | ||
Main extruder driving power | 37KW | |
Motor type | AC motor | |
Motor speed adjust the type | transducer speed adjust | |
Splitter gearbox type | grinding gear combine with skew gear for the rigid gear surface | |
d> Fixed amount feeding material system | ||
Feeding material system | automatic quantify feeding by screw | |
Screw rotation speed | 0-45r/mi | |
Motor driving | 0.75KW | |
Speed adjust method | transducer adjust | |
e> Exhausting system | ||
Vacuum pump type | water recycling vacuum pump | |
Motor power | 1.5KW | |
Vacuum degree | 0-0.075Mpa | |
B. Wood Plastic Vacuum Forming Machine |
||
Vacuum forming length | 6m | |
Material water box | tank stainless steel | |
Adjusting direction three dimensional adjust | ||
Vacuum pump driving power | 3 sets × 5.5KW, 1 set × 4KW | |
Pressure increasing pump power | 1.5KW | |
Draining pump power | 0.75KW | |
Vacuum connector | 32 pieces | |
Water connector | 32 pieces | |
Water consumption | 7m3/h | |
C. Draw-off Machine |
||
Draw-off type | rubber block drawing-off | |
Rubber block type | drawing type | |
Draw-off power | 2×1.5KW | |
Draw-off strength | 40KN | |
Draw-off speed | 0-5m/min | |
The effective length of the draw-off roller | 2200mm | |
Effective draw-off width | 240mm | |
Working pressure | 0.5-0.7Mpa | |
D.Cutting Machine |
||
Max. cutting width | 240mm | |
Cutting type | alloy saw cutting | |
Saw dia. | 400mm | |
Cutting power | 2.2KW | |
Controlling method | PLC automatically measure the length | |
E. Automatic Turning Over shelf |
||
Turning over shelf length | 6m | |
Turning over method | automatic turning over | |
Turning over material | stainless steel | |
Dimension | (L*W*H)(approx) 25×2×2m | |
Total weight | (approx) 7T |
6. WPC Board Production Line
A.Conical Double Screw Extruder Specialized for Wood Plastic
a> Screw
Material of screw | 38CrMoAlA high grade alloy steel processed by nitriding |
Screw Dia. | Φ92/188mm |
Effective length | 2500mm |
Number | 2 pieces |
Meshing type | conical meshing |
Rotation speed | 1-32.9 r/min |
Rotation direction | reverse direction outside |
Nitriding depth | 0.5-0.7mm |
Hardness degree | HV850-960 |
Surface roughness concentration | Ra≤0.8μm |
b> Hopper | |
Hopper material | 38CrMoAlA high-grade alloy steel processed by Nitriding |
Nitriding depth | 0.5-0.7mm |
Hardness degree | ≥HV940 |
Inner roughness degree | Ra≤1.6μm |
Heating method | cast-aluminum electrical heater |
Heating zone | 5 zones |
Heating power | approx 48KW |
Cooling method | cooled by blower |
Cooling power | 5×0.55KW |
c> Transporting deceleration system | |
Main extruder driving power | 110KW |
Motor type | DC motor |
Motor speed adjust the type | DC adjust speed |
Splitter gearbox type | grinding gear combine with skew gear for the rigid gear surface |
d> Fixed amount feeding material system | |
Feeding material system | automatic quantify feeding by screw |
Screw rotation speed | 0-34r/min |
Motor driving | 1.5KW |
Speed adjust method | transducer adjust |
e> Exhausting system | |
Vacuum pump type | water recycling vacuum pump |
Vacuum power | 4KW |
Vacuum degree | -0.06Mpa |
B. Wood Plastic Vacuum Forming Machine |
|
Vacuum forming length | 8000mm |
Material water box | tank stainless steel |
Adjusting direction | three dimensional |
Vacuum pump driving power | 2×11KW, 3×7.5KW |
Water pump power | 2×4KW, 2.2KW |
Vacuum connector | 60 pieces |
Water connector | 60 pieces |
Water consume | 10 m3/h |
C. Draw-off machine |
|
Draw-off type | rubber block drawing-off |
Rubber block type | drawing type |
Draw-off power | 2×5.5KW |
Max.draw-off strength | 50KN |
Draw-off speed | 0.3-3m/min |
The effective length of the draw-off roller | 1800mm |
Effective draw-off width | 1000mm |
Max. product height | 100mm |
Rubber block width | 2×490mm |
D. Cutting machine |
|
Max. cutting width | 1000mm |
Max. cutting height | 50mm |
Cutting type | alloy saw cutting |
Cutting power | 4KW |
Bit-collecting power | 1.5KW |
Controlling method | PLC automatically measure the length |
E.Automatic lift flat |
|
Lift method | electro motion |
Max. width of product | 1000mm |
7. WPC Panel Sander Model |
||
Max produce width | 1000mm | |
Min product length | 350 mm | |
Product thickness | max.160 mm | |
Transfer speed | 4-16m/min | |
Motor power of the first frame | 11kw | |
Motor power of the second frame | 7.5 kw | |
Motor power of feeding machine | 1.1 kw | |
Hardness of the first roller | 85sh | |
Hardness of the second roller | 50sh | |
Diameter of the first roller | 190mm | |
Diameter of the first roller | 140mm | |
Abrasive band dimension | 1000×1560mm | |
Working pressure | 0.55MPA~0.7MPA | |
Compressed air consumption | 14m3/h | |
Dimension | 2300 × 2500 × 2300mm | |
Weight | 4.6T |
8. Precision Engraver |
||
X travel route | 1300mm | |
Y travel route | 2500mm | |
Z travel route | 200mm | |
Processing precision | 0.05mm | |
Positioning precision | 0.05mm | |
Table structure | vacuum absorb | |
X, Y, Z | X, Y rack, Z guid screw | |
Machine self power consume | 2KW | |
Max. idle speed | 25000mm/min | |
Max. work speed | 20000mm/min | |
Main spindle energy consumption | 3KW | |
Main spindle speed | 0-24000r/min | |
Operate method | while running |
9. Panel, Profile Edge Saw |
||
Machine model | JG-WPC-CB | |
Max. travel of working platform | 2800mm | |
Max. cutting thickness | 60mm | |
Axis rotation speed of main saw | 5400/3800r/min | |
Axis dia. of main saw | 300mm | |
Main motor power | 4kw | |
Dimension | 2700 × 2900 × 800mm |
10. WPC Profile Laminating Film Machine
Laminating width | 20-300mm |
Laminating height | 125mm |
Laminating speed | 0-15m/min |
Heating power | 13kw |
Drive power | 1.5KW |
Install power | 16KW |
Dimension | 5000 × 1250 × 2300mm |
Weight | 2.5T |
11. WPC Panel Vacuum Laminating Machine
Laminating width | 50-1300mm |
Laminating height | 5-100mm |
Heating power | 32kw |
Motor power | 3kw |
Dimension | 6200 × 2200 × 2300mm |
Weight | 6T |
12. Punchy Crusher |
||
Installed capacity | 45KW | |
Crushing capacity | 700-850kg/h | |
Dimension | 1500 × 1500 × 1800mm | |
Weight | 1.5T |
13.Flour Mill of Waste Material
Dimension | 2000 × 2000 × 3000mm |
Weight | 2T |
14.Water Chiller |
|
15. Air compressor |
|
16. Mould of door panel plate |
|
Width: 1000mm |
Leave a Reply